Protecting the environment is paramount for our company. So, for our silkscreen printing we only use water-based inks.


The reasons behind this are:-
- Water-based inks are safer and better for the environment, production staff and end users.
- The inks sink into the fabric leaving no surface feel and are also very colourfast and durable when washed.
- Colours are really vibrant and can be mixed to any pantone or shade required.
- We purchase all the components for our binders, colour concentrates, water based metallic and discharge inks through just one UK-based supplier, with whom we work incredibly closely, on all aspects related to print quality, colourfastness, environmental issues etc.
We wrote a past blog detailing all about our ink REACH, ZDHC and Oeko-Tex certifications which you can read here.
But our ink is also very interesting from the perspective of how we mix thousands of colours every year. Colours which then go towards creating our customers’ beautiful printed custom tea towels, printed tote and canvas bags and printed aprons.
I started out mixing ink in my early days in the company and still find the science of colour fascinating. Developing a very accurate eye for colour takes years of experience and the ink mixing team will still call on me if they have a particularly tricky colour to formulate.
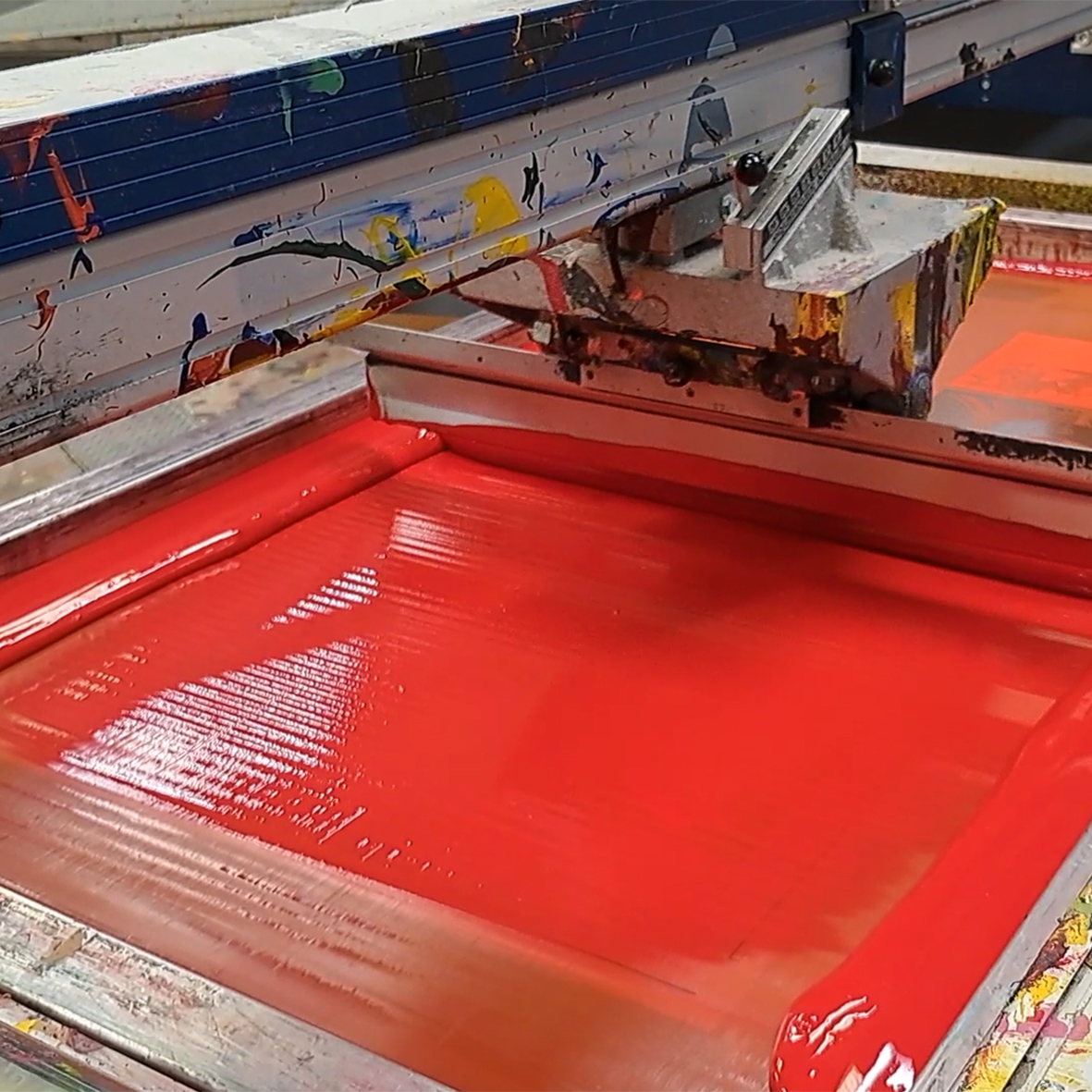
We use industry-standard colour matching systems such as Pantone Coated and Uncoated colours plus Pantone TPX (now called TPG). So, a customer can quote any of these Pantone colours and be confident that we will match their print colours to these specifications.
But not everyone has access to Pantone colours. So how else do we assist our customers with colour-matching.
Firstly, we can colour-match to the paper proofs we send out when an order is first placed.
Secondly, we can match to a supplied physical item such as a paint swatch, a piece of fabric or an existing product such as mug etc (some of the past stranger items we have been sent include a Rugby shirt and a knitted sock 😊).
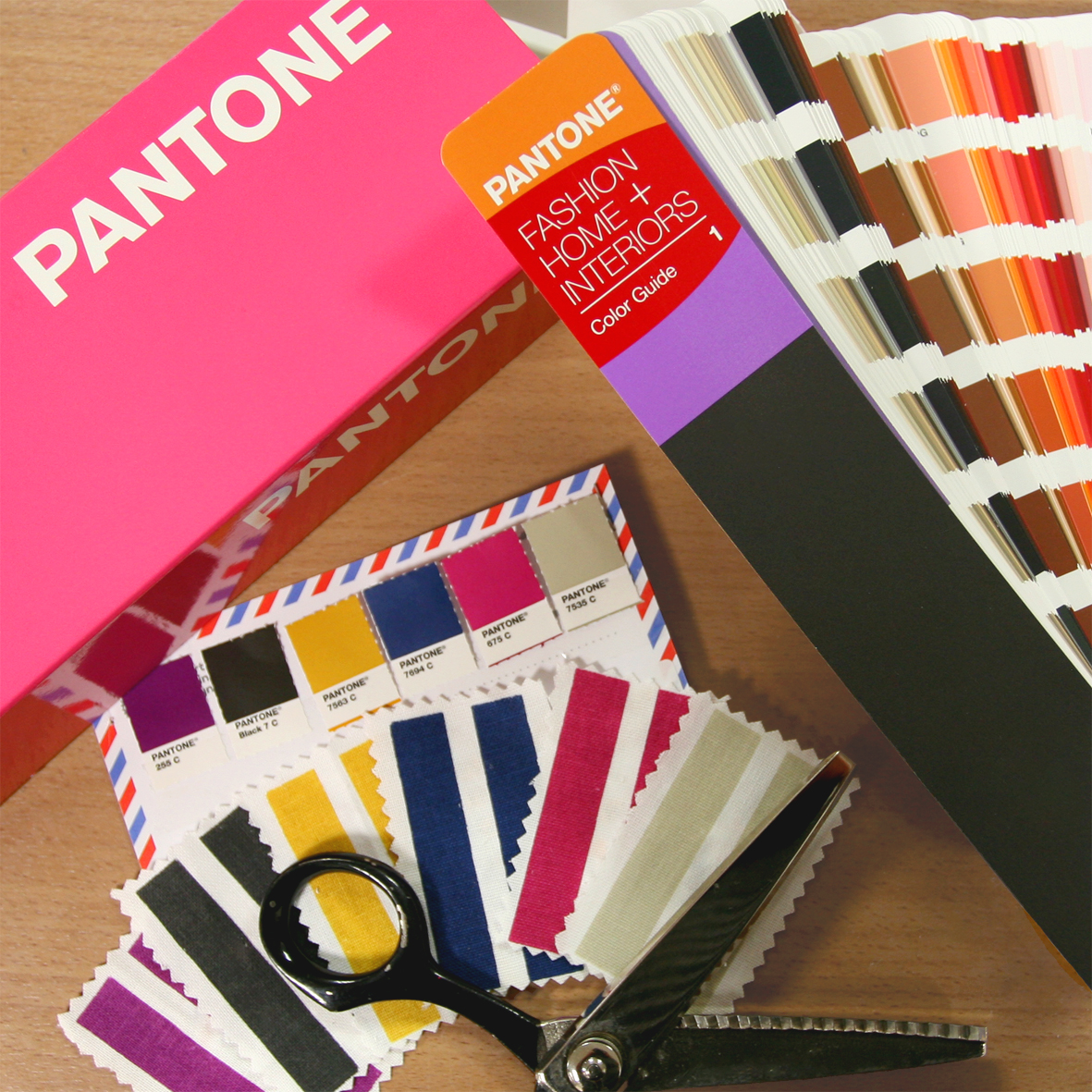
provided pantone colour-chips
We are very careful about ensuring the colours for repeat orders remain constant. We have an In-house Ink Mix Recording System on to which every customer’s record is stored. This data is used for weighing out exact amounts of the coloured concentrates, down to amounts as small as 0.1g.
We have a storeroom in which literally thousands of benchmark sample printed tea towels, custom bags, personalised aprons and custom printed cushions are stored (again all saved on a huge database). So that every time a customer orders, the sample is retrieved, and we check the colours are consistent to that first order.
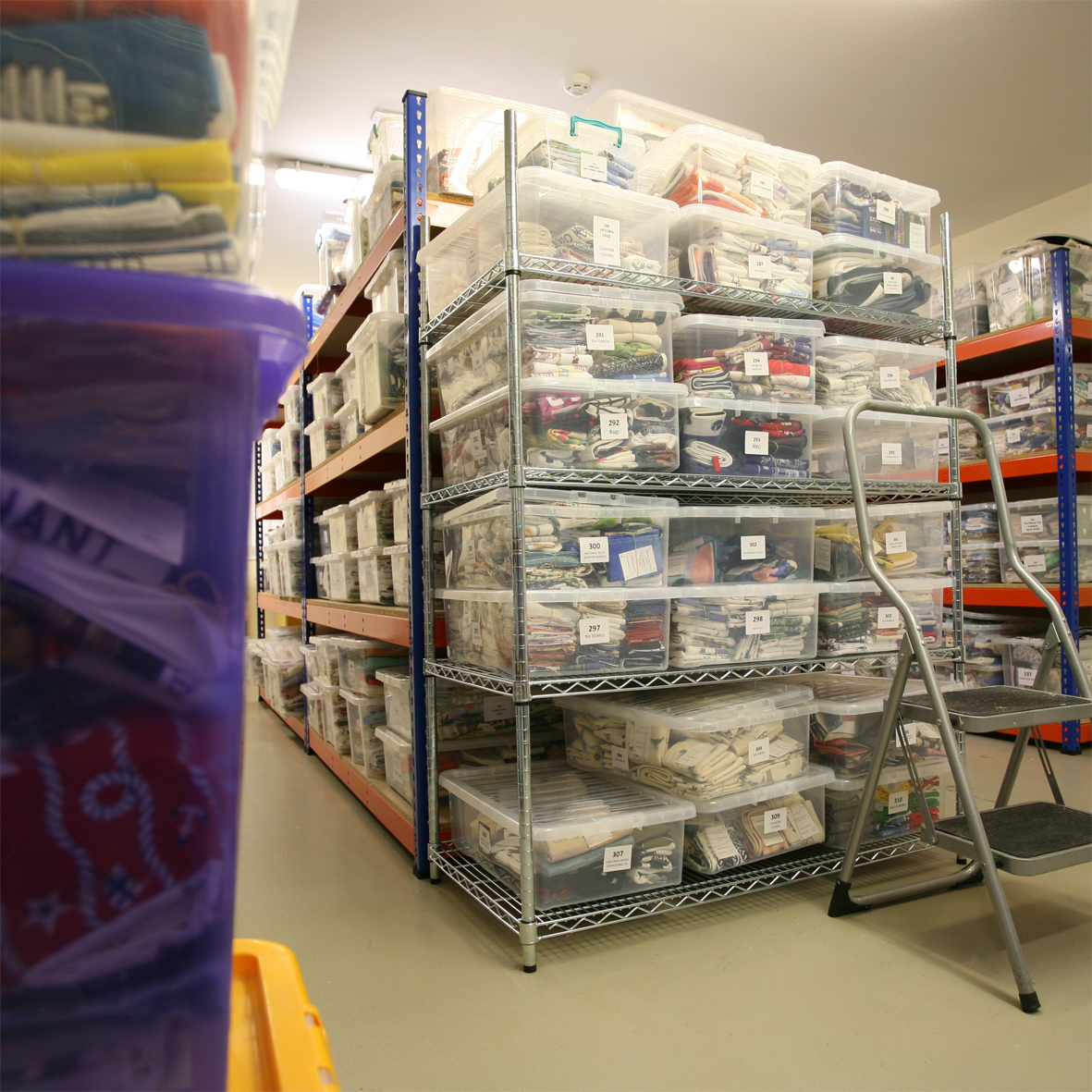
Finally mixing ink is a fun job – remember how as kids we all loved swirling poster paints together. Working with great big pots of ink is sometimes not the most pristine job in the world (we have all looked down to find a blob of ink that has mysteriously appeared from nowhere). But seeing all those separate, coloured ink concentrates swirling together to make a final unified colour, is always endlessly absorbing. So, we thought you would like to watch this short video and see the process for yourselves.
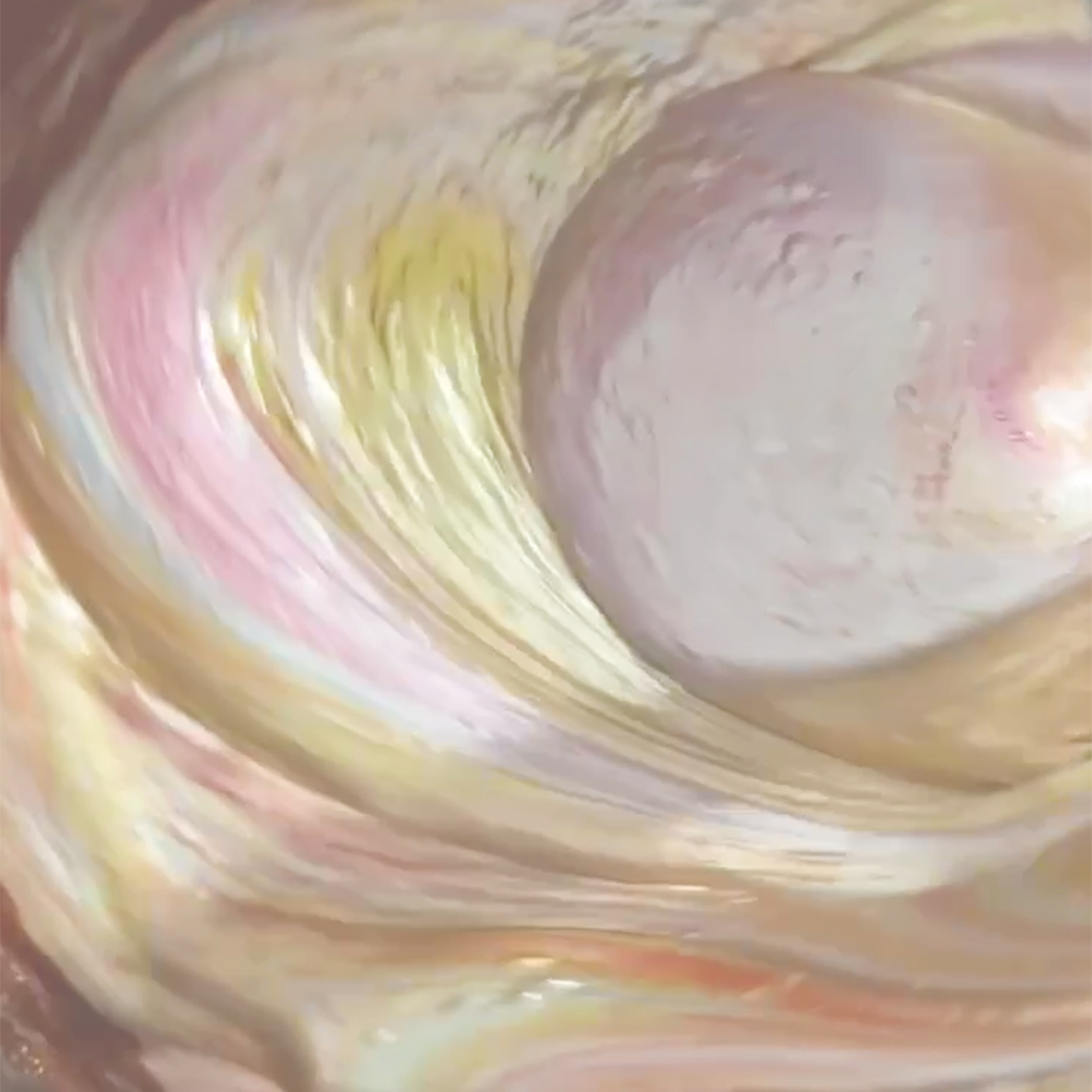
Best wishes
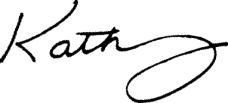
Kathy Brookes, Sales Director