Ethical & Environmental Policy

A family company, started in 1975 by our parents John and Margery Chapman, is now directed and managed by myself,
Kathy Brookes, and my brother Lawrence Chapman.
Initially the company was started with a view to helping provide employment to people with disabilities whenever possible. A
family member, son and brother, Patrick has severe learning difficulties and as a family we were very aware of the difficulties
faced by people with disabilities trying to compete for employment in the job market.
Over the years we have employed people with a wide range of disabilities and won BT’s Deaf Employer of the Year in 1994.
There is more about the history of the company on our About Us page.
The workshops where the company started were initially built in the grounds of my parent’s grade 2 listed house (formally a
Rectory). Our work has, therefore, always had an immediate impact on our actual surroundings. This has meant we have
always had a profound interest in the effects of any chemicals and processes used in the printing processes. This coupled
with the fact that we as a family have all worked long term with the various chemicals, has made us want to use processes
that are as low impact and safe as possible.
In 2005 we moved to a purpose-built factory on a local industrial estate as we had very much outgrown the original
premises. This building has been built to the highest standards regarding insulation etc thereby helping to minimise our
carbon footprint. To further our carbon reduction we also installed solar panels on the factory roof. In December 2022 we
further increased the amount of solar panels so, on a sunny day, we now create nearly 40% of the electricity we use.
For screen print, we have always specialised in water-based inks, which, although more difficult to use, have virtually no
impact on the environment.
Our supplier offers the following industry world-wide accreditations so you can be completely confident in the safety and
sustainability of our inks: the component chemicals used in the production of their products are REACH compliant.
Their eco pigments and core range products are certified to ZDHC Confidence Level 1. (The ZDHC Roadmap to Zero
programme is a coalition of fashion brands working together to eliminate hazardous chemicals in the textile printing
process).
Our supplier is Oeko-Tex certified and holds an Eco Passport (Oeko-Tex is an independent certification system for
chemicals, colourants and auxiliaries used in the textile industry).
They are GNA compliant (the GNA standard is a universal certificate of compliance and sustainability that meets customer
demand to significantly reduce the amount of hazardous and environmentally damaging chemicals in the textile printing
industry. GNA approved inks exceed the expectations of leading retail brands).
We also insist that all other chemicals used in cleaning processes etc are environmentally safe and REACH compliant.
Countryside Art Ltd is a member of SEDEX and our company is also SMETA 4 Pillar accredited.
With regard to our ethical policy over buying our fabrics: we have just two UK-based suppliers who source on our behalf and
only use selected accredited yarn suppliers and mills with whom they in turn have trusted relationships. For reasons of
commercial sensitivity we cannot openly publish the names of our suppliers on our website so we will call them Supplier 1
and Supplier 2.
Supplier 1 is SEDEX registered. (SEDEX are one of the world’s leading ethical trade service providers, working to improve
working conditions in global supply chains. They provide practical tools, services and a community network to help
companies improve their responsible and sustainable business practices, and source responsibly). Read more about
SEDEX at sedex.com
Supplier 2 is STeP audited by OEKO-TEX. (STeP by OEKO-TEX® is an independent certification system for brands,
retailers and manufacturers from the textile and leather industry. Certification is suitable for production facilities at all
processing stages who want to communicate their environmental measures externally in a credible and transparent way.
The goal of STeP is to implement environmentally friendly production processes in the long term, to improve health and
safety and to promote socially responsible working conditions at production sites). Read more about STeP by OEKO-TEX®
at oeko-tex.com
The majority of our cotton is finished and prepared for print here in the UK to our exacting specifications. Any cotton that is
finished overseas is in finishing plants overseen by our two suppliers.
We buy top quality yarn from the USA where over the years farmers have striven to reduce the amount of chemical input to
the crop, halving the amounts of pesticides used over the last 20 years. But chemicals are still needed to grow non-organic
cotton which is why we also offer a range of organic cotton options.
Most of our organic cotton is produced in India. Our organic fabrics are covered by GOTs. (GOTS is a textile production
certification that limits the use of toxic bleaches, dyes and other chemical inputs during the production process of textiles. It
is internationally recognized as the toughest organic textile standard because it goes far beyond verifying the organic
farming process to include every step of manufacturing). Read more about GOTs at global-standard.org
Supplier 1 also works with the Soil Association. (Soil Association Certification Ltd (SACL) is a not-for-profit subsidiary of the
Soil Association charity, independently providing organic certification services and advisory support on all aspects of organic
certification). Read more about the Soil Association at soilassociation.org
Finally we are asked is our cotton Fair Trade: because we feel we have taken every effort to ensure our cotton is fully
accredited and ethically produced we have not gone down the Fair Trade route – despite totally endorsing everything for
which the organisation stands. We have also not applied for Fairtrade accreditation ourselves as all our products are all
sewn here in our UK factory where we uphold the highest employment standards. Read more about Fair Trade at
fairtradecertified.org
Our pre-sewn bags are purchased from only two suppliers. Supplier 1 is a member of SEDEX and only works with factories
that are four pillar certified. Supplier 2 is Fairtrade registered.
We make sure any waste fabrics, cardboard, chemicals etc are recycled wherever possible, or disposed of responsibly
according to current legislation. 70% of all waste materials on site are either recycled or, in the case of waste cotton, used as
biomass to create energy. (Although carbon dioxide is created by this method, it is better than allowing the cotton to
decompose in landfill, where large amounts of more harmful methane gas is produced).
We are very working hard to reduce the amount of plastic we buy for our product packaging. Our aim is to continue to
drastically reduce the amount of plastic we use over the next five years. Where plastic bags are still used, we offer
alternatives such as bio-degradable plastic, plus alternatives made from other recyclable materials. The polypropylene bags
we buy are all fully recyclable and printed with the appropriate recycling logo. The vast majority of all on-site waste plastic is
now recycled.
With regards to energy usage – 38 percent of our electricity is now generated from solar panels on our factory roof. (This
enables us to save approximately 27363kg of CO2 every year). The whole factory is fitted with LED lighting and motion
sensitive switches have been installed in all relevant areas.
We have created a lovely wildlife area and pond in the factory grounds which has attracted a great deal of nature. Plus we
have planted nearly 300 trees around the factory, with more to follow this Autumn.
Finally we are also very unusual as we design, print and sew the majority of our items all under the one roof, offering quality
employment in a rural area where employment is in short supply.
By making as many items as possible in the one factory we again cut down on the environmental damage caused by
shipping goods unnecessarily from one place to another.
We also think many of our customers prefer our UK-made products because we believe in making a quality product that will
last. We cannot see the point in making a cheap product that either breaks or is not fit for purpose. That seems to be a great
waste of our planet’s resources. I still see bags we made when the company first started, over thirty years ago, being carried
around our local market town, which, I would have thought, must be some sort of record in this day and age for
sustainability.
I hope the above helps to illustrate our attitude towards our approach to business and our business dealings.
Best wishes
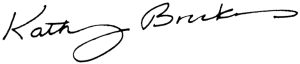
Kathy Brookes
Director